If your collision repair process involves modern vehicles, you’re already working with Advanced Driver Assistance Systems (ADAS). These systems—lane keep assist, blind spot monitoring, and adaptive cruise control—require precise recalibration after many common repairs. Whether it’s a windshield replacement, bumper repair, or wheel alignment, your shop is responsible for verifying proper ADAS system calibration before delivery.
At Minnesota ADAS Solutions, we help auto body shops like yours stay focused on repairs while we handle calibration. As a dedicated ADAS calibration center, we provide OE-standard service, a 90-minute turnaround, and clear documentation. By working with advanced ADAS calibration centers instead of investing in your own tools, you gain accuracy, efficiency, and reduced liability. If your team needs a reliable way to manage ADAS calibration without adding in-house complexity, we’re here to help. This guide outlines what an ideal ADAS calibration workflow looks like—so your shop can stay efficient, compliant, and safe.
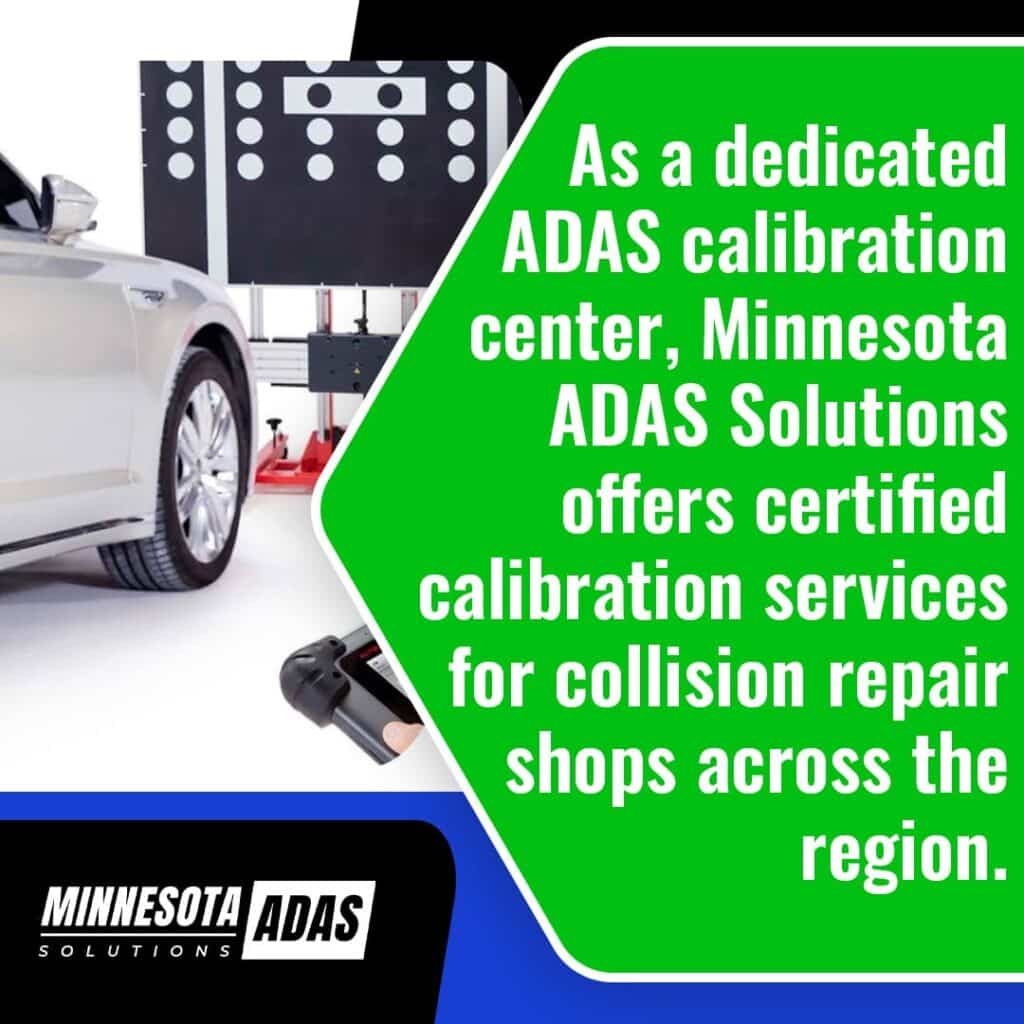
Why ADAS Calibration Matters After Collision Repairs
ADAS calibration isn’t optional for collision repair—it’s a required part of returning a vehicle to road-ready condition. If your shop repairs modern vehicles, you’re already working around sensitive sensor systems.
Modern Vehicles Rely Heavily on ADAS
Advanced Driver Assistance Systems (ADAS) are built into nearly every vehicle manufactured today. These systems handle critical safety tasks such as lane departure warnings, emergency braking, forward collision alerts, blind spot monitoring, and adaptive cruise control. To function properly, they rely on hardware like cameras, radar, and ultrasonic sensors—each installed at fixed angles and locations on the vehicle.
When even one sensor is misaligned by a few millimeters, the entire system can be thrown off. A vehicle that looks perfectly repaired could still behave unpredictably. For example, a forward collision sensor might trigger an unnecessary brake application or, worse, fail to respond when needed.
That’s why your shop can’t treat ADAS as an accessory. It’s integrated into the safety architecture of the car, and any disruption to its alignment requires full ADAS system calibration by qualified professionals.
Post-Collision Repairs Often Disrupt Sensor Alignment
Even light collision damage can impact the accuracy of ADAS sensors. Most sensor housings are mounted to components that are commonly removed or repaired in bodywork. That includes bumpers, fenders, side mirrors, and windshields. Once these parts are shifted or replaced, the sensors no longer see their environment the same way.
The change might be subtle, but the result can be dangerous. For example, a camera in the windshield that reads lane markings might no longer center properly. A radar sensor in the grille might now misjudge distances to other vehicles.
This is why your blueprinting process should include a detailed ADAS inspection. Any vehicle with these features—regardless of how minor the damage—should be routed through a qualified ADAS calibration center after repairs.
Liability and Safety Considerations for Repair Shops
Shops are liable for ADAS systems that are returned out of calibration. When a car leaves your shop, it should function as expected, and that includes all installed safety systems. If the ADAS features fail and lead to an accident, your shop could be named in the investigation. This risk grows when there’s no record showing that ADAS calibration was performed or outsourced.
Insurance carriers are also asking for detailed documentation. If you don’t provide it, you could face delays in processing claims or even disputes over the repair’s completion. Failing to verify calibration creates a gap in your repair process—one that can cost you money, credibility, and time. This is where partnering with a dedicated ADAS provider matters.
Minnesota ADAS Solutions works directly with auto body and collision repair shops across the region. We help you deliver calibrated vehicles backed by OE-based processes, quick turnaround, and complete documentation.
Common ADAS Calibration Scenarios After Collision Repair
There are several repair scenarios where Advanced Driver Assistance Systems must be recalibrated before the vehicle is returned to the customer. These situations are easy to overlook, especially when the visible damage seems minor. However, even small shifts in alignment or component replacement can interfere with sensor accuracy. Your estimators and technicians should treat these cases as routine triggers for ADAS system calibration.
Windshield Replacement
Replacing a windshield affects the field of vision for front-facing cameras. Most ADAS-equipped vehicles have a camera mounted just behind the windshield. That camera supports systems like lane departure warnings and forward collision alerts. When you replace the glass, even slight shifts in camera position can disrupt the calibration.
Bumper or Grille Repairs
Sensors mounted behind bumpers or grilles must be checked after impact repairs. Front and rear bumpers often hide radar and ultrasonic sensors. These components are responsible for features like blind spot detection, parking assistance, and rear cross-traffic alerts. If your repair includes removing, repainting, or replacing bumper covers, grilles, or brackets, those sensors can shift out of alignment.
Wheel Alignment or Suspension Work
Changes to suspension geometry impact ADAS sensor accuracy. ADAS cameras and sensors rely on known distances, angles, and heights relative to the road surface. If you’re performing a wheel alignment, changing ride height, or replacing any steering or suspension component, the position of the cameras or radars will change. That can cause the systems to misread distances or angles, triggering warnings or failing to activate.
Camera or Sensor Replacement
New ADAS components must be programmed and recalibrated. If your repair includes replacing a forward-facing camera, radar unit, or ultrasonic sensor, it’s not enough to install the part. ADAS hardware is not ready-made. Every sensor must be aimed, focused, and programmed to match the vehicle’s configuration.
Airbag Deployment
Crashes that trigger airbag deployment often impact ADAS mounting points. When airbags deploy, there’s usually significant front-end damage. This can bend or distort brackets and mounts that hold cameras and sensors in place. Even if those components appear intact, their position may have shifted slightly. That’s enough to throw off readings.
At Minnesota ADAS Solutions, we calibrate ADAS systems for all of these scenarios. Our process follows OEM procedures from start to finish, whether your shop sends the vehicle to our ADAS calibration center or uses our pickup and delivery service. We help you catch every calibration need so nothing is missed before the vehicle goes back to your customer.
What a Proper ADAS Calibration Workflow Should Look Like in Your Shop
Before you deliver a repaired vehicle, you need to verify that all safety systems are functioning. That includes every Advanced Driver Assistance System (ADAS) affected by your repair work. To do this consistently, your shop needs a defined calibration workflow.
Step 1: Identify Calibration Requirements Early
Start with a thorough review of OEM procedures during the blueprinting phase. Each manufacturer outlines when ADAS calibration is needed based on the systems installed and the repairs performed. This information is available through OEM databases, scan tools, and estimating software. Your estimators should reference these resources before any repairs begin.
Pre-scan diagnostics will flag DTCs (diagnostic trouble codes) and identify which ADAS systems are present. Combined with a visual inspection and a review of parts replaced—like windshields, bumpers, or suspension components—you’ll have a clear picture of which calibrations will be required.
Step 2: Communicate With a Trusted ADAS Calibration Partner
Work with a certified ADAS calibration center to handle the process correctly. Relying on a dedicated ADAS calibration center takes the pressure off your internal team. You don’t have to invest in costly equipment, training, or space. Instead, you gain access to certified technicians who work with manufacturer-level procedures and alignment tools.
You’ll also receive documentation that’s accurate, standardized, and ready to upload to repair management systems. This matters for insurance files, DRP audits, and customer satisfaction. Choose a partner who is local, responsive, and experienced with ADAS solution workflows that complement your production schedule.
Step 3: Schedule Calibration Without Slowing Down Production
Speed and reliability matter when ADAS calibration is part of your repair plan. Every minute counts on the production floor. When calibration holds up a delivery, your shop’s cycle time takes a hit. That impacts everything—from profitability to DRP scores.
Look for a calibration center that offers same-day or next-day availability, clear communication, and predictable turnaround. A typical static or dynamic ADAS system calibration should be completed in about 90 minutes when handled by a specialized provider.
Step 4: Documentation and Reporting
Every ADAS system calibration should include a detailed report. This documentation proves that the correct calibration was performed under the right conditions, using validated tools and target setups. It should list the systems recalibrated, include results from post-calibration scans, and confirm success with no DTCs remaining.
You’ll want to retain these reports for every vehicle. They support your repair documentation, protect you during insurance reviews, and offer clear proof of work to your customers.
Minnesota ADAS Solutions works with collision repair shops across Minnesota to streamline this entire process. We help you stay on schedule, meet documentation standards, and avoid the guesswork around ADAS system calibration—all without disrupting your workflow.
How Minnesota ADAS Solutions Integrates With Your Collision Repair Process
Collision shops that handle late-model vehicles every day are already seeing how Advanced Driver Assistance Systems (ADAS) affect post-repair decisions. You’re not just restoring body panels—you’re responsible for returning critical safety systems back to function. That’s where we come in.
Certified ADAS Calibration Without the Investment
You don’t need to buy specialized tools or dedicate floor space to calibrations. Minnesota ADAS Solutions is an advanced ADAS calibration center that performs precise calibrations for all major makes and models. We handle the full calibration process, so your shop doesn’t need to invest in high-cost targets, alignment systems, or dedicated bays. Our facility is purpose-built for accurate, manufacturer-specific calibrations. Every technician on our team is trained in OEM repair procedures and uses tools that are validated by the original equipment manufacturers. This approach allows your shop to offer complete ADAS solutions while focusing your in-house team on structural, mechanical, and cosmetic repairs.
Pickup and Delivery Options
We offer flexible options that include pickup and delivery from your shop. This reduces the need for your staff to transport vehicles, eliminates scheduling backlogs, and helps you make better use of limited space. Shops operating at high volumes benefit most from this flexibility. Whether you’re managing multiple DRPs or juggling internal deadlines, our mobile and transport services adapt to your schedule.
Fast Turnaround and Accurate Results
Most calibrations are completed and returned to you in about 90 minutes. We built our workflow to support production environments. Our calibration process is efficient, with a strict focus on system accuracy. We pre-scan, perform the required calibration (static or dynamic), verify success with post-scan diagnostics, and deliver a full report for your records. This allows your shop to hit delivery targets without sacrificing quality. It also reduces the chance of returns, rework, or missed steps that can create liability.
OE-Standard Calibration Methods
We use manufacturer-specific procedures, targets, and setups for each make and model. This includes correct floor leveling, lighting conditions, distance measurements, and environmental setup for both static and dynamic calibrations. You can trust that every vehicle is calibrated to manufacturer specifications, backed by clear documentation and consistent results. That includes proof of calibration completion, successful scans, and a record of all ADAS features calibrated.
Benefits to Your Shop and Customers
Advanced Driver Assistance Systems are now standard on most late-model vehicles. If you’re handling structural or cosmetic repairs, you’re already touching components that affect how these systems perform. ADAS calibration isn’t a separate step—it’s part of a complete repair. Here’s how proper ADAS system calibration benefits both your shop and your customers.
Improved Safety Outcomes
Customers receive vehicles with fully functioning ADAS features. Systems like automatic emergency braking, lane-keeping assist, and adaptive cruise control rely on precise calibration to function. If these systems aren’t calibrated after repairs, they may fail to activate—or worse, respond unpredictably.
When your shop returns vehicles with fully calibrated ADAS, you’re helping customers drive away with confidence that their safety systems are active and functioning properly. This level of precision reflects directly on the quality of your repair work.
Reduce Comebacks and Insurance Friction
Incomplete ADAS system calibrations can lead to failed inspections or new claims. If a vehicle leaves your facility without proper ADAS calibration, it could fail a post-repair inspection or come back due to a warning light, system malfunction, or a customer complaint. This creates unnecessary delays, added labor, and possible tension with insurers or adjusters.
By documenting each calibration with a detailed report, you’re creating a clear record that supports the accuracy of your repair. This protects your business and avoids disputes that slow down claims or damage customer trust.
Boost Reputation and Customer Trust
Offering ADAS calibration builds trust and positions your shop as a leader in modern repair standards. When you include ADAS system calibration as a documented part of your workflow, it sends a clear message. Your shop is equipped to handle the demands of modern vehicles. You’re not guessing about system performance—you’re verifying it.
That builds trust with both individual customers and referral partners. It also gives your team an edge in DRP relationships where documentation, speed, and completeness all matter.
At Minnesota ADAS Solutions, based in Bloomington, MN, we help your shop meet these expectations with every calibration we perform. You get reliable results, fast turnaround, and a level of support that reinforces your shop’s reputation for quality and safety.
Partner With Minnesota ADAS Solutions for Reliable ADAS Calibration Near You
ADAS calibration is no longer optional—it’s essential. Collision shops that service modern vehicles must treat ADAS as part of the structural repair process, not a separate service. Whether you’re dealing with a windshield replacement, bumper repair, or suspension work, verifying ADAS system performance is critical for safety, compliance, and customer satisfaction.
At Minnesota ADAS Solutions, we make it easy for your shop to maintain high standards without slowing down production. Our advanced ADAS calibration center is built for precision, speed, and documentation—so you can deliver road-ready vehicles with confidence. Most calibrations are completed in 90 minutes, supported by validated tools, OEM-based procedures, and transparent reporting.
You don’t have to buy equipment or train in-house techs. Just call, schedule online, or use our pickup and delivery options. If you’re searching for ADAS calibration near you, we’re the trusted partner that collision repair professionals throughout Minnesota rely on.
Contact Minnesota ADAS Solutions at (612) 425-4230 or email us at info@mnadas.com.
Schedule your next calibration and keep your shop moving with confidence.